When to Rebuild vs. Replace: Making the Call on Aging Construction Equipment
Is your construction equipment past its prime? Learn when to rebuild vs. replace aging machines to avoid downtime and costly repairs.
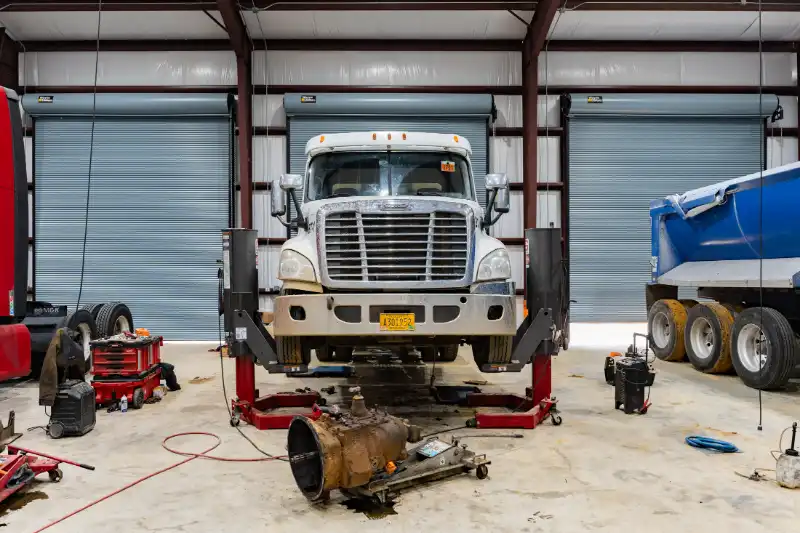
No matter how tough your equipment is, nothing lasts forever—not even your most dependable excavator, wheel loader, or haul truck. Eventually, every contractor, operator, or fleet manager must confront a critical question: Should I rebuild this machine, or is it time to replace it?
While this decision may appear straightforward, the reality is much more intricate. Opting for the wrong choice can result in excessive downtime, compliance issues, or significant capital expenditures. Making a wise choice can prolong the life of your fleet, optimize budget allocations, and ensure that job sites in Oakland, Riverside, and Los Angeles operate efficiently.
This article provides a framework to help you determine when a rebuild is the smarter investment—and when it’s time to move on.
The Hidden Costs of Keeping Equipment Too Long
It’s easy to fall into the trap of thinking, “It still runs, so why replace it?” However, aging construction equipment often becomes a financial burden long before it entirely breaks down. Here's why:
- Unpredictable failures bring job sites to a standstill.
- Fuel inefficiency drains operating budgets.
- Outdated safety features create liability.
- Emissions noncompliance in California can lead to costly fines.
- Operator dissatisfaction leads to higher turnover or performance issues.
In high-demand areas like Los Angeles and the Bay Area, reliability and efficiency are non-negotiable. An unreliable dozer or backhoe can grind a significant development project to a halt.
When a Rebuild Is the Right Call
A component or full machine rebuild can be a cost-effective alternative to buying new equipment, especially when carried out by experienced diesel technicians who are familiar with your make and model. Here are scenarios where a rebuild makes sense:
1. The Frame and Chassis Are Structurally Sound
If the undercarriage, frame, boom, and body exhibit minimal signs of fatigue or damage, overhauling the engine, hydraulic system, or drivetrain can restore performance at a fraction of the replacement cost.
2. The Equipment Has Low Annual Utilization
Machines used for seasonal or intermittent work, such as trenchers or graders, may not warrant the investment in new equipment. A targeted rebuild can keep them job-ready without the upfront cost of a new model.
3. High-Value or Specialized Equipment
Some construction equipment is custom-fitted or specifically designed for particular tasks. Replacing these units may entail months of lead time and substantial investments in the six figures. In such scenarios, a rebuild is frequently the only feasible option.
4. Readily Available Parts and Expertise
For machines with readily accessible OEM or aftermarket parts and diagnostic data, a rebuild becomes considerably more economical. Partnering with an experienced shop like Fleetworks, which services Oakland, Riverside, and Los Angeles, ensures minimal guesswork and a quick turnaround.
Key Rebuild Targets That Deliver ROI
A rebuild doesn’t always involve stripping the machine down to the frame. Often, rebuilding at the component level provides significant improvements in performance and longevity.
- Engine Overhaul – Refreshes the combustion system, pistons, liners, injectors, and bearings.
- Transmission and Torque Converter – Restores gear response and hydraulic power transfer.
- Hydraulic System – Replaces worn pumps, seals, and control valves to bring back full cycle speed.
- Undercarriage – Tracks, rollers, and idlers can be swapped to prevent premature wear on the chassis.
A phased rebuilding strategy can extend limited budgets while gradually restoring functionality.
When It’s Time to Replace the Equipment
No machine lasts forever, and in some cases, continuing to rebuild aging equipment is like patching a sinking ship. Here's when replacement is likely the smarter financial move:
1. Excessive Hours with No Major Overhauls
Machines that have logged over 12,000 to 15,000 hours, particularly without significant rebuilds, are often on borrowed time. At this stage, several systems are likely worn, and cumulative repair costs may surpass 50% of a new unit’s value.
2. Frequent Unplanned Downtime
If your machine is frequently visiting the repair shop, it’s no longer supporting your workflow—it's hindering it. When your teams in L.A. or Oakland can’t depend on the equipment, productivity and profitability suffer.
3. Struggles with Regulatory Compliance
California’s emissions standards are among the most stringent in the U.S. Older machines that do not meet CARB Tier 4 Final standards can result in fines, restrictions on job bidding, and limitations on operations, particularly in air quality management districts such as South Coast AQMD and Bay Area AQMD.
4. Poor Fuel Efficiency
Older diesel machines generally have higher fuel consumption rates, which can quietly deplete operating budgets, particularly on long-duration jobs. Upgrading to a newer, more efficient unit may result in a better total cost of ownership, despite the higher upfront costs.
Comparing Costs: Rebuild vs. Replace
Let’s put real numbers to the decision.
If a rebuild can restore 70–80% of the machine’s performance and lifespan for less than half the cost of a new model, it’s often a better investment. However, when multiple rebuilds are required simultaneously, or if a core component (such as the frame or transmission housing) is compromised, replacement becomes the safer long-term option.
Considerations Unique to California Fleets
Construction equipment operating in California encounters a different set of pressures compared to other provinces.
- Stricter emissions enforcement
- Increased urban job site density
- Higher fuel and insurance costs
- Union safety requirements and inspections
Operators in Los Angeles, Riverside, and Oakland may also be influenced by local ordinances or job site regulations that limit the use of outdated or non-compliant equipment.
Additionally, many cities are encouraging fleet upgrades through Clean Air Grants or CARB modernization rebates. If you’re considering a replacement, it may be worthwhile to explore fleet credit or provincial funding options to inform your decision.
Don’t Overlook Operator Input
Often, the individuals with the most direct insight into a machine’s health are those who use it on a daily basis. If your team consistently reports:
- Sluggish hydraulic response
- Difficulty with ignition or gear shifts
- Overheating under normal load
- Poor visibility or ergonomics
…it’s worth listening to. Operator feedback can act as a canary in the coal mine for larger systemic issues.
Rebuild Strategically, Replace When Necessary
There is no one-size-fits-all solution for extending the life of your construction fleet. The choice to rebuild or replace necessitates a comprehensive perspective that considers condition, utilization, compliance, repair history, and total cost of ownership.
At Fleetworks, we offer comprehensive inspections and cost analysis to help you determine the most effective course of action. Whether you're managing a site in Los Angeles, dispatching from Oakland, or overseeing projects in Riverside, our skilled team ensures you make a decision that supports long-term performance and profitability.
Do you require expert advice on whether your machine is worth rebuilding or should be replaced? Schedule an on-site inspection with Fleetworks. Our team in Oakland, Los Angeles, and Riverside delivers precise diagnostics, detailed cost breakdowns, and compliance insights—allowing you to make informed decisions with confidence.
Shop Locations
Fleetworks Inc. is proud to have expanded to three locations across California, providing a wide-range of truck & equipment repair & fleet services from our locations in Oakland, Santa Fe Springs, Riverside, & the surrounding areas.
Santa Fe Springs Location
14011 Marquardt Ave, Santa Fe Springs, CA 90670
Riverside Location
*Equipment Service & Repairs only*
1310 Dodson Way, Riverside CA, 92507